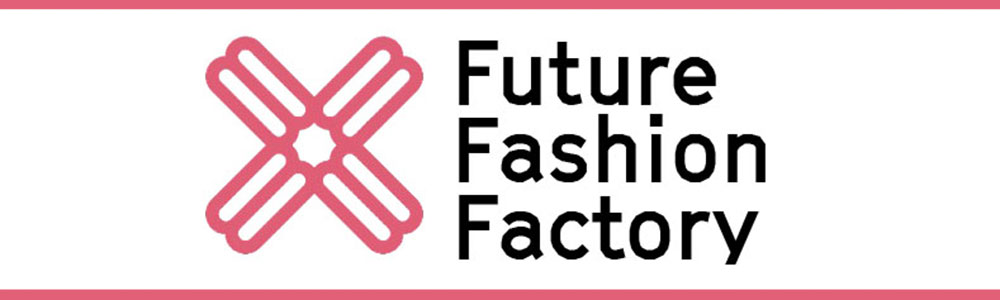
An investment of over £2 million has now been secured for innovation in the fashion and textile industry over Future Fashion Factory’s first three funding calls.
Future Fashion Factory is an industry-led programme in which designers lead a highly creative process of applying, co-developing and then implementing new textile and industrial digital technologies (IDTs). The initiative is in collaboration with supply chain manufacturers and retailers together with other technology experts in the high-value luxury textile and fashion sector.
Thirteen additional collaborative research and development (R&D) projects have now been approved in the Programme’s third Innovation Funding Call, supporting independent designers, heritage Yorkshire mills and fashion tech companies.
Each project addresses a challenge identified by Future Fashion Factory’s community of over 270 fashion businesses and professionals. From new AR/VR/MR experiences of high-value fashion and textiles through to more sustainable materials and designs for outerwear and footwear.
Future Fashion Factory is part of the Creative Industries Clusters Programme; an £80 million initiative led by the Arts and Humanities Research Council (AHRC), part of UK Research and Innovation (UKRI). The Programme is led by the University of Leeds in partnership with the University of Huddersfield and Royal College of Art.
Successful projects in this call include:
-
A new digital system for 3D-woven fashion design – Twelve Oaks Software
3D weaving is enabling a new frontier for the design and manufacture of personalised fashion and accessories. Enabling designers to creatively harness the potential of this technology requires co-creation of new digital systems that are responsive to user needs. This project is exploring the requirements of designers and each stage of the fashion supply chain to support the development of a new digital 3D-woven design system. The work embeds digital thinking as part of the product development process for 3D woven garment production; exploring the systems required to support designer-manufacturer-consumer relationships.
-
An AI-driven planning system for producing luxury fabrics – Abraham Moon & Son
Major global fashion brands rely on luxury fabric manufacturers to create their most iconic looks. This project will develop a new AI-driven planning system for Abraham Moon’s vertical woollen mill. The project aims to improve the end-to-end scheduling processes within operations. Therefore increasing the company’s agility, improving lead-times and reducing inventory.
-
Customisable, comfortable and effective British wool face coverings with defined filter performance – British Wool
This project focusses on the design and manufacture of new personalised, reusable face coverings as fashion accessories, with specified filtration characteristics combined with excellent thermo-physical comfort and aesthetics. The R&D is harnessing British-grown wool as a sustainable resource, fibre functionalisation technology and short, UK manufacturing supply chains, to deliver long-lasting high quality, face-covering products that also reduce the environmental impacts of end-of-life disposal.
-
Digital technologies for lead-time and waste reduction in the colouration of luxury fabrics – DP Dyers
In piece dyeing fabrics for fashion and interiors, highly skilled dyers use their creative judgment to devise a dye recipe to achieve the required shade. Making late-stage adjustments to this recipe to ensure consistency is costly and time-consuming. It also leads to waste when fabrics do not meet quality standards. A new ‘digital assistant’ is being developed to support the dyeing and shade-matching process. This enables DP Dyers to rapidly provide fashion businesses with consistent, high-quality dyed fabric that also produces minimal waste.
-
A radical approach to more sustainable cotton production – hydroCotton
Cotton is a staple of the global fashion industry. Growing and producing in a chemically intensive way requires large volumes of water. It also requires significant land usage. hydroCotton’s innovative approach to sustainable cotton farming radically decreases these environmental stresses. It reduces water usage by up to 80% while increasing yield and fibre quality. This project will design and manufacture new harvesting and fibre processing approaches. It will also evaluate hydroCotton fibre and yarn properties against conventional cotton fibre. Plus, produce prototype garments using this new form of sustainably farmed cotton in 2021.
-
High-quality virtual garment simulation from blockbuster movies to digital fashion – Numerion Software
Digital communication has become more crucial than ever in the fashion industry. Designers and manufacturers are collaborating remotely while consumers further embrace online retail. Based on a market-leading garment simulation tool used by major movie studios, this project is validating a new cloud-hosted, virtual 3D garment visualisation service. It will allow consumers and designers to engage with different looks and styles on a webpage as part of an AR/VR/MR experience. The new platform aims to reduce product lead times and waste from sampling as well as customer return rates.
-
A sustainable coloration system to reduce the environmental impact of adding colour and pattern to fashion products - Rose Danford-Philips
Colour and pattern are essential elements of a fashion designer’s creative toolkit. However, the way we apply them to fashion materials is widely criticised for its use of water, chemical and energy resources. Going back to the chemistry of the natural sources of pigments, this project will develop a sustainable coloration system for clothing and accessories.
-
A new advanced and circular material for watersports using nylon from waste garments whilst mitigating micro plastic leaching – RubyMoon Gym to Swim
This initiative will explore the separation of nylon from elastane in the most environmentally friendly way; creating a new sustainable material for both swimwear and sportswear using waste nylon. It will seek to develop a superior yarn that mitigates microplastic shedding that pollutes our air, oceans and soil. It will also reduce the demand for virgin materials.
-
A vegan, petroleum and freshwater-free alternative to down or polyester for insulated clothing – SaltyCo
Modern textiles manufacturing consumes huge amounts of freshwater. It also emits massive quantities of CO2 and produces enough waste to fill a garbage truck every second. SaltyCo uses saline agriculture techniques to grow fibre-bearing plants that can thrive in seawater. This enables the production of the first ‘freshwater-free’ natural fibre textiles. This project will evaluate and benchmark the physical properties of the new fibres. Furthermore, it will prototype new filling materials for insulated clothing such as jackets and coats. Therefore providing a vegan and petroleum-free alternative to down or polyester.
-
Colour-based machine learning to create new pathways for designers seeking inspiration in visual databases – Visualist
Visualist is a modern productivity suite for creatives. The platform helps designers to both centralise and make sense of visual inspiration. Most databases rely on keyword searches and text metadata to retrieve appropriate results. However, this method often misses the subjective nature of visual images. This project will develop machine learning (AI) techniques to form new connections between images based on their colour palettes. Therefore providing a platform for a linked visual database and for building new pathways for designers to navigate when seeking inspiration.
-
Closed-loop manufacturing of customisable, sustainable, made-to-measure footwear – Vivobarefoot
Vivobarefoot produces regenerative footwear to make feet stronger. It uses wide, thin and flexible design principles that allow feet to do their natural thing. This Vivobarefoot led project will use a new approach for digitally-driven design and manufacture of customisable, made-to-measure, 3D-printed shoes; improving fit while also reducing waste and shortening lead times. By exploring recovery, recycling and re-use of materials from shoe products at the end-of-life, Vivobarefoot will help lay the foundations for a more sustainable shoe industry.
Commenting is Professor Stephen Russell, director of Future Fashion Factory.
“This year has presented a unique set of challenges for the fashion and textile industry, requiring a raft of new solutions while accelerating changes that were already underway, not least digitalisation. We had a fantastic response to this funding call, which shows the appetite for innovation among UK businesses. By supporting these exciting projects, we want to pave the way for continued growth and resilience in the UK’s world-renowned luxury fashion industry.”
For further information on Future Fashion Factory, please click here.