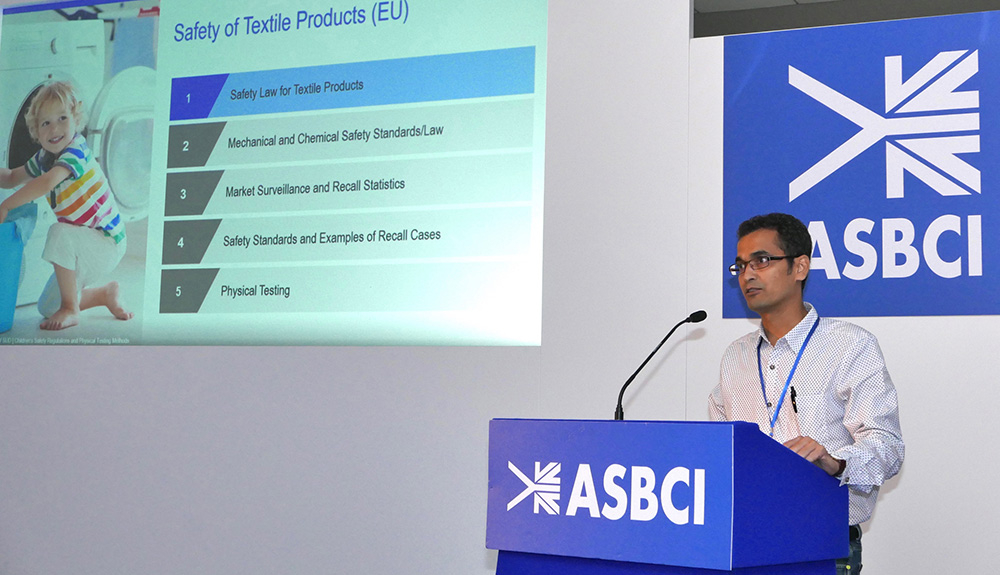
The importance of hazard identification in product design, understanding foreseeable use, and mitigating the commercial risks of global supply chains were just some of the topics discussed at a technical seminar on effective risk management organised by the ASBCI and sponsored by TÜV SÜD, a global testing and certifications provider.
The ASBCI’s latest technical seminar opened with a comprehensive overview of product safety regulations. This was provided by keynote speaker Sheikh Minhazuddin, deputy general manager for R&D, technical governance and regulatory compliance at TÜV SÜD.
Minhazuddin discussed the responsibilities of product manufacturers with regards to putting safe products on the market, particularly childrenswear. He looked at recall statistics, identifying the most common reasons for product recalls – strangulation, choking and chemical hazards – and detailed relevant standard updates.
He also addressed specific risks in-depth. Going on to explain the hazards of certain design features and product categories and also what can be done by industry to reduce the number of incidents.
Sarah Anderson from M&S provided a detailed look at the importance of hazard assessment to control risk in childrenswear.
Anderson explained why an understanding of child development is the starting point for developing safe products. She then ran through the different stages of development and the hazards associated with the exploration strategies children use. This ranged from choking and strangulation to suffocation, ingestion, insertion, laceration, irritation, restriction of vision and toxicity. Also, possible mitigation strategies.
Meanwhile, industry consultant Geraldine Cosh delivered an entertaining presentation focusing on giving delegates the knowledge and tools to conduct both risk and hazard assessments effectively. She discussed using multiple resources to identify potential hazards including injury databases, social media and recall reports. Also, how these combine to determine foreseeable use.
“If someone is doing it on YouTube, it is a foreseeable use. Then you have to ask yourself: is it reasonable, and do you have to mitigate it?”
Building on this, Cosh led an interactive workshop session challenging delegates to conduct a hazard assessment on various products. For example, a mermaid tail, a baby’s sleepsuit, a sequin top and a pair of summer shoes. The question was: would you sell this product?
As well as discussing the hazards identified during the exercise, groups considered ways they could be designed out. Also, whether the issues amounted to non-compliance or simply an unsatisfactory product.
Additionally, Cosh highlighted useful tools for risk and hazard assessments.
Firstly, the GPSD risk assessment guidelines. The Commission Decision 2010/15/EU provides a flowchart on how to conduct a risk assessment.
Also, the NEISS database. Cosh recommends this tool to everyone doing risk assessments. You can download a year’s worth of data at a time in Excel spreadsheets and search by product type etc. This is US data. There is European data, but it is harder to use and not product focused. NEISS is all about consumer products.
In the US a consumer can go on the Safer Products website and report problems; 65% of reports for clothing are injuries. Manufacturers and retailers can then respond. Cosh describes this as a “great resources for risk assessments”, with all information being free to access.
Finally, Recall data. Recall guidance document PAS 7100 is free for SMEs.
Geoffrey Willis, international senior apparel industry specialist from Trigon, also spoke at the seminar.
Willis discussed the commercial risks facing clothing brands in the era of offshore sourcing; particularly the loss of control over manufacturing and the consequent loss of manufacturing knowledge amongst buyers.
He argued that the most effective strategy to combat sourcing risks is to ensure you have a thorough understanding of the capabilities of factories. He outlined an assessment method that covers everything from facilities and processes, production performance and planning through to quality, human resources, materials sourcing and service.
“You wouldn’t buy a house without a survey, so why would you use a factory without doing this?”
Concluding the day was a Q&A session, where delegates put their questions to an expert panel. This included seminar speakers as well as risk assessment experts Alan Ross from HSTTS/MTS and Ian Strudwick from Shirley Technologies. Questions included how to use product safety standards and guidance documents. Also, reconciling the need for constant innovation with product safety and the point at which foreseeable use becomes misuse.
“People will always find stupid things to do with products,’ says Cosh. “If you found yourself in court, would you feel comfortable saying you had done everything you could?”
Commenting on the more interactive format of the seminar is ASBCI chairman, Alistair Knox. “In addition to excellent presentations from our expert speakers, we saw active and animated discussion among delegates in the workshop session and a lively Q&A. There was a recognition that everyone shares the same problem; the challenge of creating a product that will do no harm. It was a great networking opportunity for everyone involved.”
Claire Franco, global technical account manager at TÜV SÜD, also adds; “It has been a pleasure to work with the ASBCI and speakers on an amazing event. The day brought together various risk assessment approaches and resources. From looking at concepts, to what to look for and ask of potential factories, to how consumers foreseeably interact with and use products, and how these steps can be tailored to meet the requirements of businesses.”
About the ASBCI
The Association of Suppliers to the British Clothing Industry (ASBCI) is a not-for-profit organisation. Its membership represents all key sectors of the clothing and textile supply chain.
Formed in 1973, it is the only forum of its kind where component suppliers and fabric producers can exchange ideas and knowledge with designers, retailers and garment cleaning specialists.